OPERATIONAL AND PROCESSING SUPPORT
CLIENT
Underground Paste Plant
OBJECTIVE
Core Crew was engaged to provide comprehensive operational and processing support for the Paste Plant operators during the commissioning phase and ramp up into production. Our team was tasked with acting as the client representative, offering hands-on assistance with operations, training site personnel, and supporting ongoing maintenance.
CHALLENGES
The client faced several hurdles in their efforts to launch and maintain operations at the paste plant.
- Operational inexperience | The paste plant was brand new, with no operational procedures in place. Operators lacked experience in running day-to-day operations and didn’t have the frameworks to operate within.
- Training gaps | The operators needed training not only in plant operation but also in quality control procedures to ensure consistent and efficient performance.
- Staff shortages | Recruitment practices led to delays in hiring personnel, further compounding operational challenges.
- Maintenance challenges | The team needed to identify the required maintenance regime including daily maintenance requirements, as well as scope out tasks that were beyond the plant’s internal capabilities.
- Commissioning delays | The commissioning phase was delayed due to incomplete construction, creating uncertainty around the plant’s timeline.
OUR APPROACH
Core Crew worked with our partners Xenco Services to scope out the required support and deploy a skilled team of operators, project leads, and a maintenance supervisor to support the client in the following areas:
- Procedures | Helped develop and validate their operating procedures, including the QA/QC procedures and then trained their operators in the safe operation of the plant.
- Training | Ensured operators were equipped with the skills required for safe and efficient operations. This was led through formal Training VOC’s and on the job training by our experienced operators.
- Operational readiness support | We established maintenance routines, critical parts and spares identification and shutdown requirements. This was documented and built into the CMMS.
- Maintenance execution & quality control | Training included the proper operation of paste plant equipment, as well as the identification of shutdown requirements and replacement instructions for key components like filter belts.
- Reporting & feedback | We developed a system for structured reporting and feedback to the client to ensure transparency and accountability. This fed into the site management operating system.
RESULTS
The collaboration between Core Crew and Xenco Services enabled the client to successfully overcome their challenges, launch operations, and establish a solid foundation for ongoing success. This foundation was built on a structured and disciplined approach in the key operational areas of:
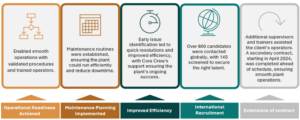
This project highlights Core Crew’s dedication to delivering practical, hands-on solutions that address operational challenges and ensure smooth, efficient operations from day one. Working seamlessly alongside Xenco Services, Core Crew exceeded client expectations, providing the best possible solutions tailored to their needs.